Robotic Welding Fixtures: Design Tips and Best Practices
Robotic Welding Fixtures: Design Tips and Best Practices
Read the blog post from our partner Hirebotics- it eloquently outlines the synergy between quick and affordable fixture production and robotic welding
"Just-In-Time" Manufacturing
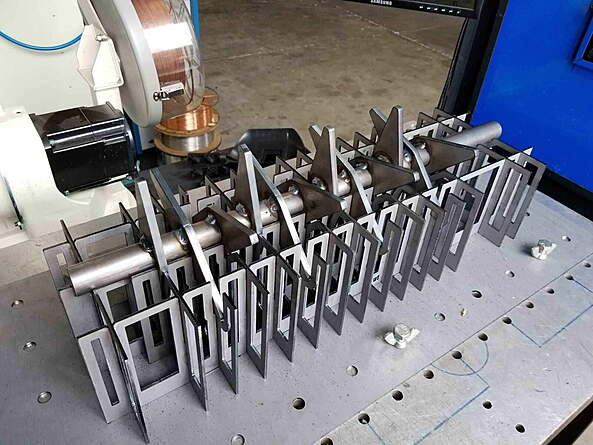
Welding fixtures can be expensive and complicated to design – and sometimes a product of simple luck and flaw. For manufacturers, the question is often “How fast can I get a fixture, at what cost and for what return?”. In this "just-in-time" (JIT) production world, short runs are becoming common. So, when fixturing can be done in part or in total using a quick and cheap manufacturing process, bidding on such jobs becomes attractive.
Welding Fixture Design and Staffing Bottlenecks
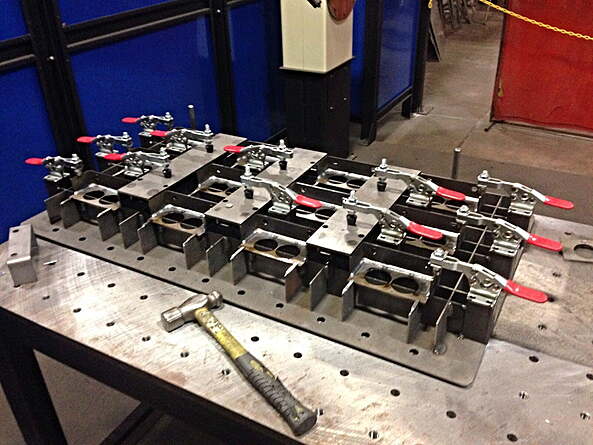
When the demand for fixtures outweighs the manpower at hand, outsourcing the design for fixtures becomes attractive, our solution is likewise affordable.
Our tool designers consult with you about your fixture needs using online tools to do virtual meetings along with email and telephone calls. We are with you every step of the way.
Our solution uses our proprietary software solution generates the geometry for welding fixtures for cutting from flat sheet metal. Like a 3D jigsaw, fixture components must interlock to create a part fixture. While you could use SOLIDWORKS™ or similar, it requires time (staff), effort and most likely some subsequent manual editing.
Adapting Existing Processes for Fixturing
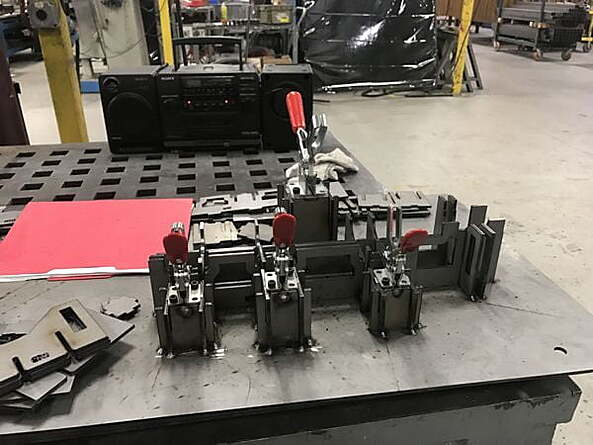
Hard tooling for traditional fixtures often depends on costly milling and other “non-sheet metal” processes. So, how can this be minimized? The simple answer is to marry the processes and machinery you already have‒ lasers, waterjets, punch presses, etc. ‒ to the appropriate CAD system. We provide the electronic data files for you to cut out in your shop or at a local sub-contractor.
Smarter Welding with Fixture Design
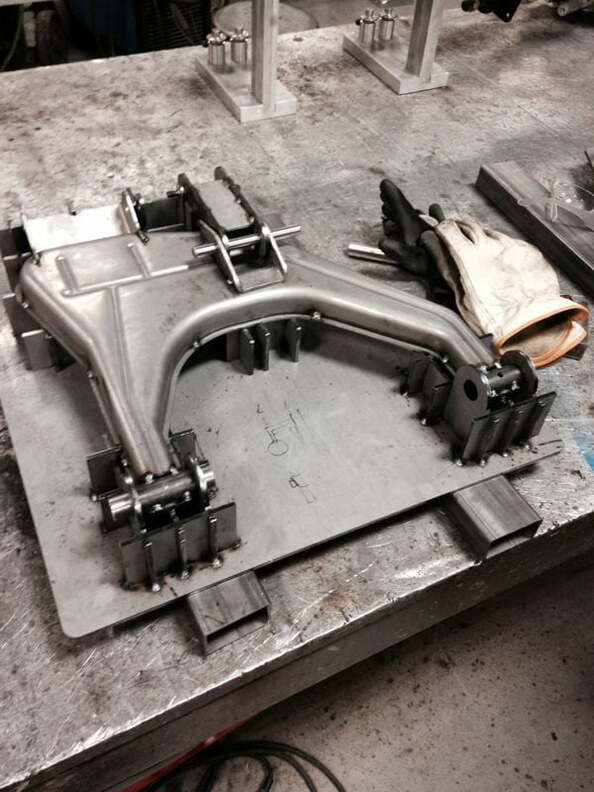
- Conduct a short run without a robot, using a precious manpower to do the welding and make or source an expensive fixture.
- Conduct a short run with a robot sitting idle while an expensive fixture is made or sourced.
Upstream Changes
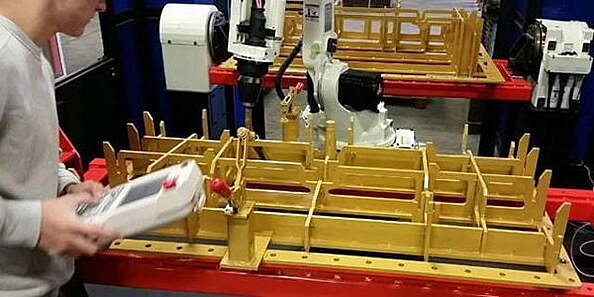
Standardization, Reducing Storage Space
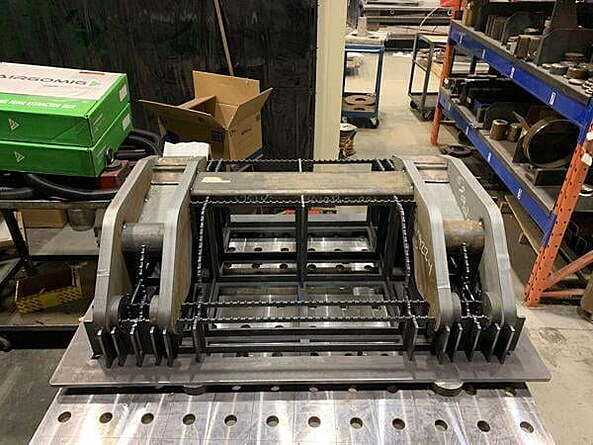
Cost Savings with our Welding Fixture Design
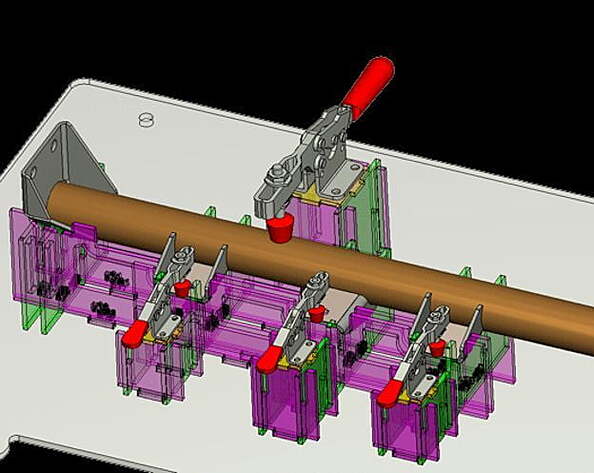
Watch one of our fixtures in action
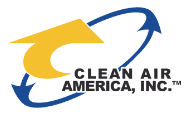
Below is an example of a two step fixture courtesy of Clean Air America. The righthand station is the initial tacking fixture, the other the full weld-out process.
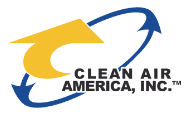
Below is an example of a two step fixture courtesy of Clean Air America. The righthand station is the initial tacking fixture, the other the full weld-out process.
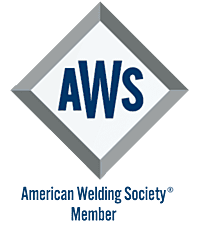