Wire EDM Programming Software with OPTICAM for SolidWorks: Enhance Precision and Productivity
Everything. Automatically.
Work natively inside SOLIDWORKS(TM)
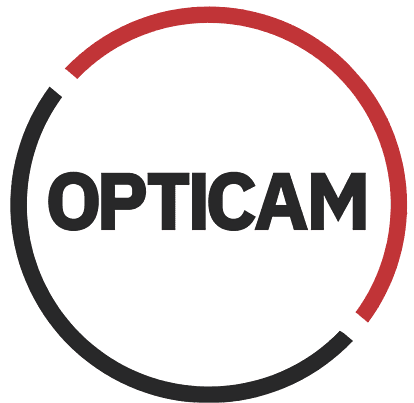
Get to know OPTICAM Wire EDM Programming
Product Manager - Melanie Staib - outlines the features and benefits of OPTICAM Wire EDM Programming
(4 minutes, 35-second video).
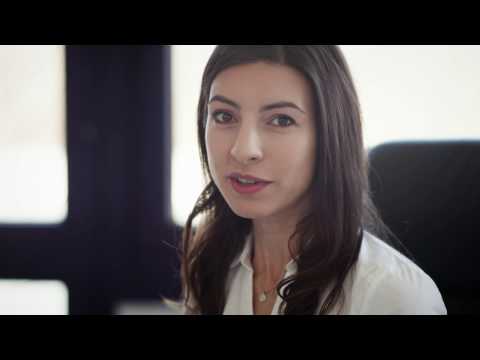
Wire EDM Programming Software Highlights
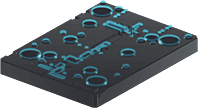
Analysis and implementation – according to your wishes.
OPTICAM analyses the parts recognises wireable geometries and creates their machining features simultaneously. The tool paths are shown graphically and follow subsequent changes of the model immediately or can be manipulated afterwards. In the case of incorrect data, the automatic geometry recognition can be influenced by entering a tolerance. Faces or edges can also be chosen manually for the wire EDM of only specific areas or for the creation of user-defined features. Furthermore, integrated technologies and machining strategies can be assigned directly to the created machining features.
- Direct, parametric machining on 3D faces and solid data
- Graphical offset display by direct model linking
- Manual feature creation
- Using feature information
- Undercut control
- Maximum conicity control

Recognising and assigning – for a quick solution.
OPTICAM assigns the correct machining functions automatically to the recognized features.
- Cylindrical machining
- Constant and variable taper, also on cylindrical parts
- Ruled surface machining with automatic synchronization
- Inclined machining
- Collar machining
- Subsequent positioning of a taper despite cylindrical construction (constant, variable or as collar machining)
- Pocketing
- Variable Reference Plane Height
- Automatic threading and cutting off of the wire
- Diagonal threading
- Automatic positioning
- Automatic clustering of identical geometries
- Multi-part programming
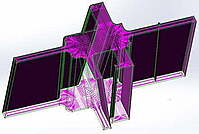
To avoid manual interventions and machine downtimes, an efficient pocketing of the geometries without the creation of slugs is often needed. OPTICAM offers special strategies for this purpose:
- Cylindrical and conical pocketing
- Ruled surface pocketing *
- Partial pocketing of geometry sections *
* These modules are optionally available.
The Feature Recognition places the start holes at the best possible position automatically; it is also possible to modify this position at a later time. If there are already predefined start hole geometries, the Feature Recognition takes them into account. Furthermore, type, position and number of tags can be defined automatically or manually. Thus it is also possible to create triangular and multiple tags with several start holes.
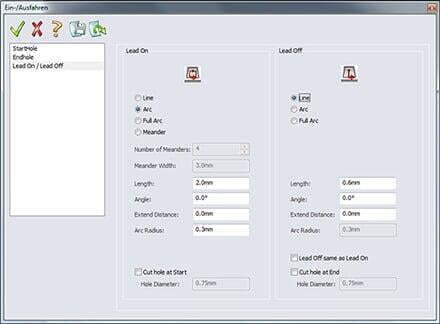
With just a few clicks the lead on and lead off strategies can be set or influenced.
- Straight, at an angle/arc- and meander-shaped
- Possibility to over travel the contour
- Lead on and lead off technologies programmable
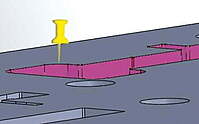
Events can be placed at any position of a feature. Comments or machine instructions, e.g. M-codes, G-codes or arbitrary NC-sets can be inserted at these points. Furthermore, individual features can be split up into several segments. For each segment the number of cuts, offset values, lead on and lead off technologies or a partial pocketing can be set separately.
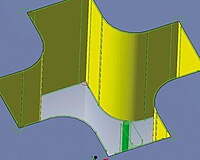
Five types of corner reliefs allow a specific control of the tool path in sharp corners without changing the model. This is especially important in cutting tool manufacturing.
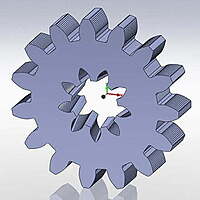
With the OPTICAM Gear module it is possible to create non-standard gears. Profile shifts, tip and root radii, changing the tip and root diameter and the creation of the gears via roller distances or via the mass across teeth are possible options.
The Gear module is optionally available.
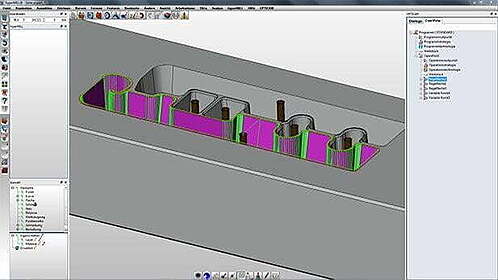
Cut by cut towards the optimum – for a safe and efficient operation.
OPTICAM contains all the machining strategies which are required for the efficient and safe operation of wire EDM machines. All cuts are shown in the cuts dialog and can be changed afterwards.
- Strategies for attended and unattended day and night operation
- Punch strategies
- Reverse cutting
- Automatic cutting off of slugs
- User defined operation strategies can be saved as template
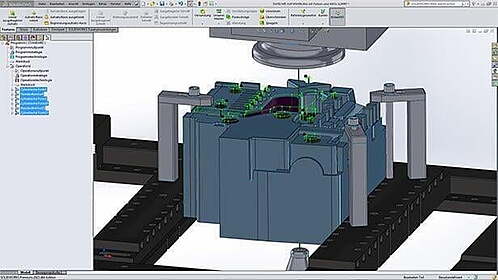
Developing tool paths is good – control is better.
A 3D simulation with material removal was inserted to ensure a safe tool path check. Besides the offsetting, fixture plates and the machine heads are also displayed.
- Collision- and demoldability check
- Maximum taper angle and UV deflection check
- Calculation of the cutting time
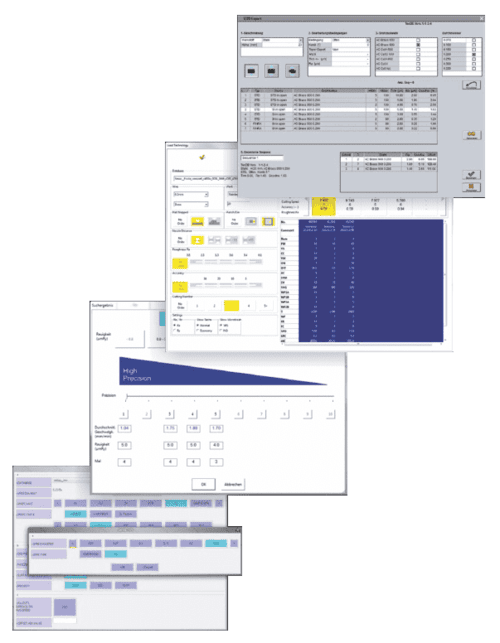
For all products and models – and for your specific requirements.
OPTICAM offers original technology databases for all common manufacturers. The user can either access the machine databases directly via interfaces, import the machine databases himself or is provided with a database which has already been converted.
- AC CUT 20/30/200/300/400/E350/E600
- Mitsubishi
- Fanuc
- Sodick
- Makino
- ONA
- MSeibu/Seibu
- Excetek
- AccuteX
- Joemars
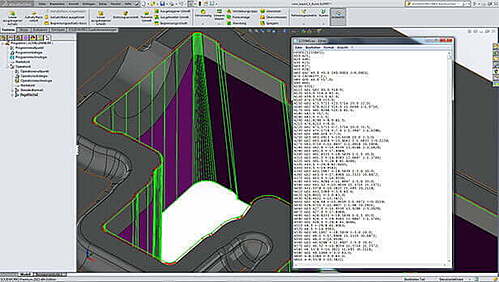
Always up-to-date – for the sake of your success.
OPTICAM has been developed in cooperation with leading machine manufacturers and is being continuously adjusted to the latest functions of the wire EDM machines. High-quality postprocessors and integrated technology databases are available for all products and types of machines.
Product Datasheet
Click the tile to the left to download a product datasheet in PDF format.
Wire EDM FAQ |
Wire EDM is most commonly used in mold and die manufacturing processes, particularly for extrusion dies and blanking punches. EDM can be used in everything from prototypes to full production runs, and is most often used to manufacture metal components and tools.
When using standard 0.010" diameter brass wire you can expect a consistent, reliable wire EDM cutting speed of approximately eighteen to twenty inch/hour.
While accuracies of +/- 0.00004” (0.001mm) are sometimes quoted for wire EDM, +/- 0.0002” (0.005mm) is more widely accepted. The reality is that EDM accuracy depends on a combination of workpiece characteristics, the surface finish desired, and the time available for machining.
Virtually any conductive material can be cut using Wire EDM. This would include all metals, including steel, aluminum, brass, titanium, polycrystalline diamond and alloys and superalloys of all types.
Any conductive material can be wire EDM machined, including aluminum, brass, carbide, copper, hastalloy, inconel, steel, stellite, and titanium.
Wire EDM machining works by creating an electrical discharge between the wire or the electrode and the work piece.It is in fact “contactless” machining - the wire does not touch the surface. Due to the inherent properties of the process, Wire EDM can easily machine complex parts and precision components out of hard conductive materials.
An EDM surface finish is different to one produced by conventional material removal processes. Rather than exhibiting directionality, the texture is random, which is beneficial in many applications. Furthermore, by taking multiple skimming passes, EDM finish quality can become almost mirror-like.
- Conventional EDM Machines. Conventional EDM also goes by several other names, such as sinker EDM, die sinking, cavity-type EDM, volume EDM and ram EDM.
- Wire EDM Machines. Wire EDM, also known as spark EDM, wire burning and wire erosion, uses a thin heated wire as an electrode.