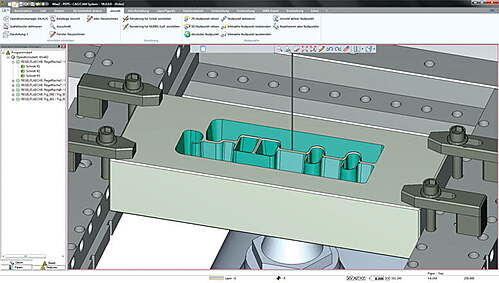
Continuously Developed By Our Wire EDM Programming Software Team
The PEPS / OPTICAM Classic Wire EDM module has been developed in cooperation with leading machine manufacturers and is being continuously adjusted to the latest functions of the wire EDM machines. The advanced capabilities of the product make it the market leader in this field, and it is recommended by many machine manufacturers.
- Projection Wizard for the automatic creation of Z-constant geometries
- Simulation including offsetting, demoldability and collision checking
- Automatic threading, cutting off and positioning of the wire
- Automatic calculation of the start position including start hole output
- Constant and variable taper
- Ruled surface machining
- Undercut control
- Inclined machining
- Tapered and cylindrical pocketing
- Automatic cutting off of slugs
- Triangular and multiple tags
- Section offsetting
- Variable Reference Plane Height
- Technology databases for all common machine types
- Lead On and Lead Off technology
- Operation strategies can be completely saved
Wire EDM Programming Software Highlights | Optimization in all fields of application.
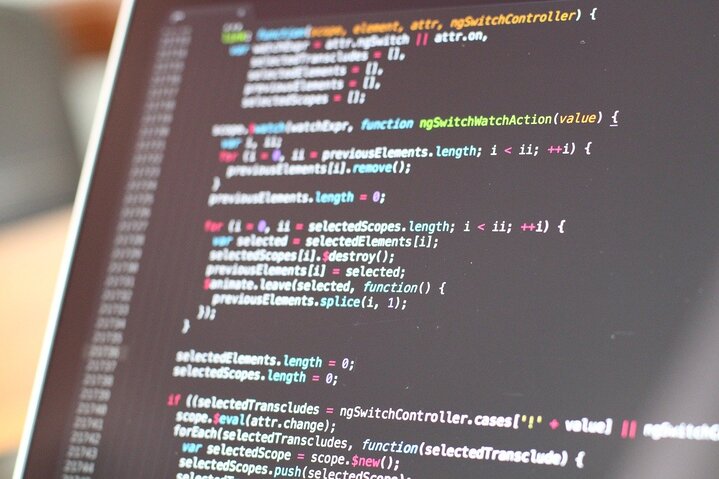